Material properties Element
|
Description
|
MAT1LS lets you define a linearly elastic, isotropic material model for NLFE elements that follows Hooke’s law. This material employs a linear strain model.
|
Format
|
<MAT1S
id = "integer"
e = "real"
nu = "real"
rho = "real"
YS = "real"
AP = "integer"
/>
|
Attributes
|
id
|
Unique material property identification number.
|
e
|
Young’s modulus for the element.
|
nu
|
Poisson’s ratio for the element. Default is 0.0.
|
rho
|
Element density.
|
YS
|
An elastic limit for strain. Default is 0.0.
YS >= 0.0
|
AP
|
Selector for the elastic model used. Default is 1.
|
Comments
|
1. | This material element defines a linearly elastic, isotropic material that obeys the Hooke’s law. Each element must have a unique material identification number. |
2. | In this approach, the stress-strain relationship is . The strain components are defined as |

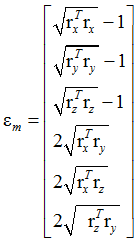
3. | The difference between MAT1 and MAT1LS lies in the definition of strain – compared to MAT1, the use of this material model may result in less accuracy, but this material model is computationally more efficient. |
4. | YS lets you specify a maximum limit on the elastic strain that the component is allowed. If, during the simulation, the component strain (at any element in the component) exceeds this value, MotionSolve issues a warning message. |
5. | AP is a selector that allows you to choose the elastic model that is used to calculate the internal resistance of the NLFE component. The following approaches are available for the BEAM (BEAM12 and BEAMC) elements: |
Approach (AP)
|
Description
|
AP=”1”
|
Continuum mechanics approach.
|
AP=”2”
|
Elastic line approach.
|
AP=”3”
|
Euler Bernoulli beam theory,
|
AP=”4”
|
Timoshenko beam theory.
|
|
Example
|
The example demonstrates the definition of a MAT1LS element.
<MAT1LS id="1" e="2.07e+5" nu="0.3" rho="7.810e-6" YS="0.002" AP="2"/>
|