Use this tool to create solid elements with variable thickness depending on the ply thickness and continuum shell properties assigned to them. The options that are supported include:
• | Solids for each ply: The number of solids in the thickness direction is equal to the number of plies with wedge elements to fill the gaps when plies overlap. |
• | Single solid for all of the plies, but variable thickness depending on the total ply stack thickness. |
• | Multi layer solids: A single solid is created for a given group of plies. The total number of plies are separated using dummy layers and solid elements are created for each ply group. |
Note: | This tool is supported for Nastran, Abaqus and OptiStruct solvers. |
|
1. | Develop a composite shell model with Shell_section_composite property. Stop the procedure with ply realization. Do not convert the ply to a zone based model using laminate realize. |
2. | Change the 3D element type to SC8R and SC6R in the 3D subpanel on the Element Types panel. This will assign continuum shell properties to the newly created solids. |
3. | Use the Shell to Solid Conversion dialog to select either Create solids for each layer or Create single solids for all layers. |
4. | Select Current Collector from the Component drop down. |
5. | Check the Fill gaps option for Create solids for each layer. |
6. | Check the Delete Shells option. |
7. | Check the Create Props option. |
8. | Select all of the plies and click Convert. This creates a solid composite. You can see the ply direction, even on the new solid elements. |
Note: | If you create single solids for all layers, discontinuous elements may be created near the ply drop off areas. These nodes should be equivalenced to pass the solver runs. |
|
|
1. | Develop a composite shell model with Shell_section_composite property. Stop the procedure with ply realization. Do not convert the ply to a zone based model using laminate realize. |
2. | Change the 3D element type to SC8R and SC6R in the 3D subpanel on the Element Types panel. This will assign continuum shell properties to the newly created solids. |
3. | Create dummy plies (zero thickness, zero ply angle) to separate the plies into a group. You are also required to create top and bottom dummy plies in addition to the separation dummy plies. Dummy plies can be created using the Edit Ply dialog and assigning all the elements in the model to that dummy ply so that it runs through the entire model. |
4. | Next, the dummy plies need to be assigned to the laminate. It is required to add top and bottom dummy plies in addition to inserting separation dummy plies. This is accomplished using the Edit Laminate dialog. |
5. | Select Shell To Solid Conversion from the Aerospace menu to open the Shell to Solid Conversion dialog. For Solid Elems select Create multiple solids using dummy ply separation. The Fill gaps checkbox is automatically selected as long as you define the top and bottom extra dummy plies in the laminate in addition to the separation dummy plies. |
6. | Select the laminate that is required to be converted and then click Convert. |
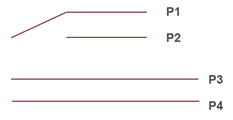
|
|
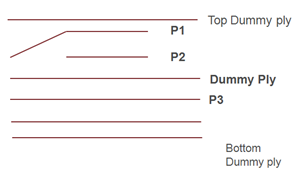
|
Original shell model plies
|
|
|
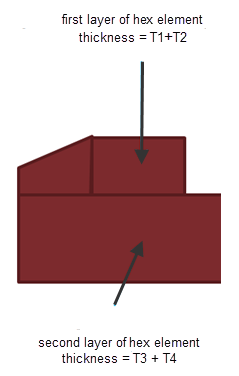
Updated shell model plies
|
See Also:
Aerospace Menu